25일 일본 아이치현 도요타시 모토마치 공장 내에 위치한 GR 팩토리. 차체(바디) 공정에서 3차원 카메라가 달린 로봇팔이 쉴새 없이 차량의 구석구석을 사진 찍고 있다. 이 로봇팔이 수집한 3D 계측 데이터는 해석 시스템에 저장된다. 데이터 해석 시스템은 설계도를 바탕으로 가장 적합한 부품의 조합을 선택하고 공정 작업을 지시한다.
같은 부품이라도 ㎜ 단위의 생산 오차가 생기기 마련이다. 만일 부품마다 오차가 1㎜씩 발생한다면 수만 개의 부품으로 이뤄진 자동차의 최종 오차는 어마어마하게 커진다. 이를 '제로(0)'로 줄이기 위해 도요타 GR 팩토리는 3D 카메라를 통해 부품과 차체의 오차를 측정하고 각 차에 맞는 부품의 조합을 골라 조립한다. 이 때문에 일반 자동차 공장의 한 공정당 걸리는 시간이 30초 내외라면 GR 공장은 하나의 공정을 거치는데 최대 9분이 걸린다.
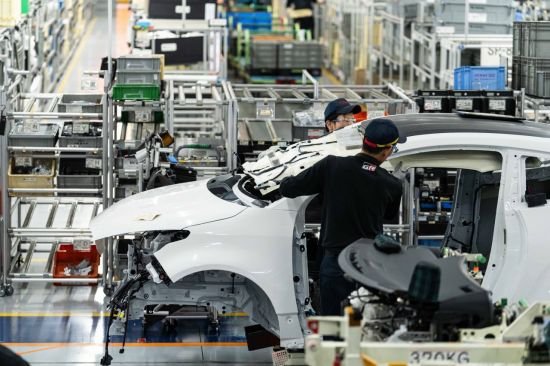
도요타는 GR 고성능 차량의 강성을 높이기 위해 용접 포인트와 고강성 접착제 사용을 늘렸다. 대표적인 고성능 차량 GR 야리스는 전장이 4m밖에 되지 않는 소형차지만 접착제를 사용하는 부분의 길이는 무려 35m에 달한다. 또한 강화하고자 하는 포인트에 특화 용접을 하는데, 이 용접 포인트를 3700여곳에서 최근 4500곳까지 늘렸다.
이날 공장에서는 차체(바디)와 하부를 결합하는 과정도 볼 수 있었다. 하늘색 안전모와 팔토시, 보호안경, 안전화를 착용한 작업자 4명이 차량 1대에 달라붙어 작업하고 있었다. 보통 다른 공장에서는 커다란 기계가 차체를 들어 올리고 아래에서 하부 프레임이 만나며 순식간에 결합된다. 하지만 GR 공장에선 첨단 기기를 사용하는 동시에 대부분의 작업은 사람의 마지막 손길을 거친다. 이 때문에 GR 야리스, GR 코롤라, LBX 모리조 RR 등 3개 차종을 생산하는 GR 팩토리의 생산량은 하루 100여대 정도로 제한된다.
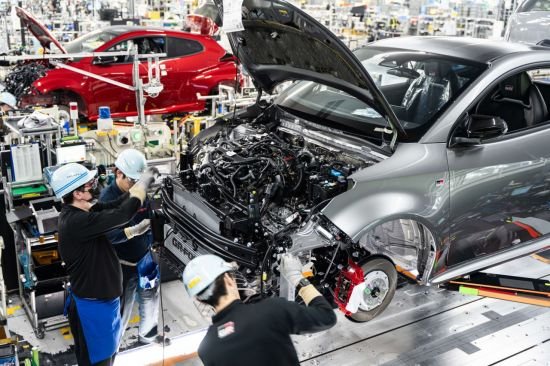
마지막 검사 공정으로 이동해 휠 얼라인먼트(바퀴 정렬) 하는 모습을 살펴봤다. 모든 조립과 외관 검사가 끝난 차량은 동그란 턴테이블 위에 올라와 방향 전환을 하게 되는데, 출고 전 핸들의 꺾어짐을 최소화하기 위해서다. 휠 얼라인먼트 기기 위에 차량이 올라오면 사람이 차량 아래에서 직접 손으로 조정을 한다. 모니터에 4바퀴의 정렬 정도를 나타내는 숫자가 소수점으로 나타나고 오차범위에 들어오도록 정렬이 완료되면 초록색으로 바뀐다.
모든 검사가 끝난 고성능 차량은 바깥에 있는 테스트 드라이브 코스에서 시험 주행을 한다. 일반 양산차는 일부 차량만 테스트를 하지만 고성능 차의 경우 출고되는 모든 차량을 시험 주행한다. 공장 주변의 왕복 6㎞ 코스를 돌아보면서 전문 테스트 드라이버가 20가지 정도의 항목을 점검한다. 토요타 관계자는 "GR 팩토리는 고강성 바디와 고정밀도 하부를 갖춘 스포츠카를 생산하기 위한 전용 공장으로 만들어졌다"며 "컨베이어 벨트가 없어 생산 차종이나 생산량, 생산 기술이 달라져도 언제든 생산 라인을 교체할 수 있다"고 말했다.
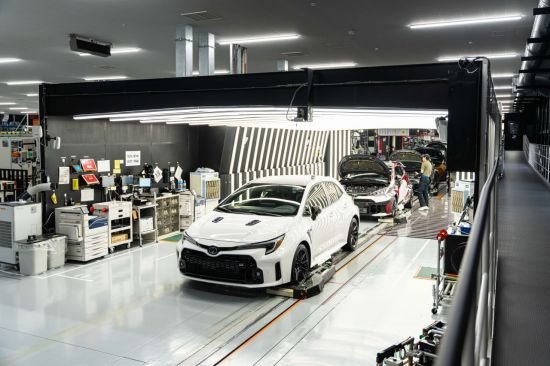
도요타(일본)=우수연 기자 [email protected] <ⓒ투자가를 위한 경제콘텐츠 플랫폼, 아시아경제 무단전재 배포금지> |